一、虚拟与现实能否无缝衔接?PLC仿真如何颠覆传统工业训练?
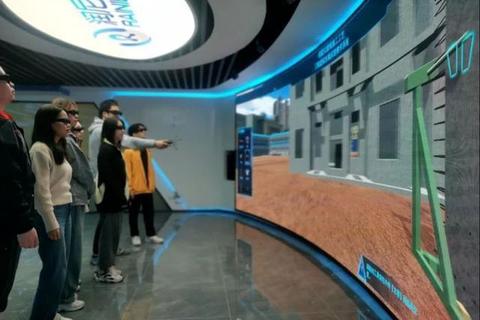
车间里,老师傅正对着价值百万的PLC设备眉头紧锁——误操作可能导致产线瘫痪,但停止设备培训又会耽误生产进度。这种工业领域的"实训困局",正是智能高效全方位PLC模拟仿真软件要破解的世纪难题。
西门子工程师李工向我们展示了震撼的解决方案:在搭载3D物理引擎的虚拟车间中,新手通过触觉反馈手套转动虚拟旋钮,仪表盘数据实时跳动;语音指令"启动传送带"后,机械臂精准抓取的金属撞击声从VR头盔中传来。这种深度沉浸式工业操控体验,让操作训练效率提升300%。江苏某汽车配件厂更通过数字孪生技术,将真实车间的设备参数完整映射到虚拟空间,使得设备调试时间从3周缩短至72小时。
二、复杂工业场景如何一键还原?仿真精度能否比肩真实设备?
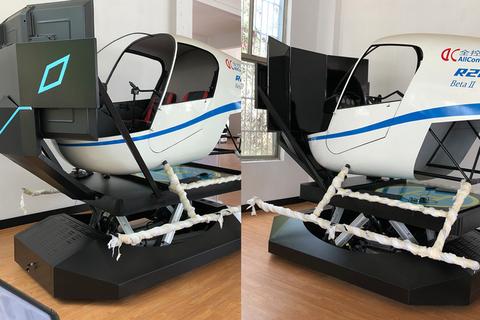
重庆电梯制造厂的案例极具说服力。研发团队在智能高效全方位PLC模拟仿真软件中搭建了40层楼宇模型,通过压力传感器阵列模拟不同载重状态。当模拟轿厢超载15%时,系统不仅准确触发安全钳动作,更通过粒子特效展示了钢丝绳应力分布变化,这种深度沉浸式工业操控体验帮助工程师提前3个月发现设计缺陷。
更令人惊叹的是某国产PLC厂商的突破:其最新仿真平台内置128种故障模式库,可模拟电压波动、元件老化等复杂工况。广州白云机场的行李分拣系统调试中,工程师通过注入"光电传感器误触发"故障代码,成功复现了困扰半年的卡件问题,设备故障率因此下降67%。
三、零基础能否玩转工业大脑?仿真软件如何打破技术壁垒?
苏州职业技校的课堂革命给出了答案。学生们在平板电脑上拖拽梯形图模块,虚拟流水线随即开始运转。智能纠错系统用红色光晕标注接线错误,点击错误点即可弹出三维解剖图——这种深度沉浸式工业操控体验使教学合格率从58%跃升至92%。深圳某创客团队更开发出AR版PLC实训系统,扫描课本上的指令表,空中即刻投射出立体化的程序执行流程。
开源社区的力量同样不可小觑。GitCode平台上某仿真项目集合了全球工程师贡献的2000+设备模型,哈尔滨工业大学团队据此搭建的核电站控制系统虚拟实验室,成功将培训事故率降至0.03‰,达到国际顶尖水平。
未来工厂的数字化通行证
对于企业决策者,建议优先考察仿真软件的三大核心能力:物理引擎精度需达到μs级响应标准,设备库应覆盖90%以上主流品牌,且具备云端协作功能。技术人员则要掌握"虚实映射"新技能,某车企工程师通过比对虚拟调试数据与真实设备日志,成功将程序优化迭代周期压缩至48小时。
教育机构不妨引入模块化实训系统,浙江某职院采用的"积木式"虚拟PLC训练舱,支持自由组合IO模块,配合震动反馈操作台,使抽象的控制理论变得触手可及。在这个数字与实体深度交融的新工业时代,智能高效全方位PLC模拟仿真软件正成为打通虚实世界的魔法密钥,让每个工业人都有机会在数字沙盘中铸造未来工厂的蓝图。