传统工业如何跨入智能时代?三菱给出破局答案
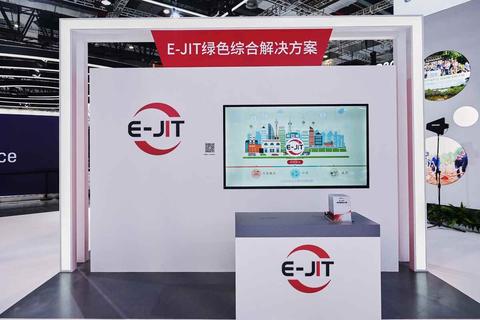
当某汽车工厂的机械臂突然停机,损失每分钟超过十万元;当制药企业因设备参数偏差导致整批原料报废;当电度系统无法实时响应新能源波动……这些真实场景暴露出传统工业的致命短板——智能化程度不足。全球制造业正面临转型阵痛,三菱电机用三十年技术积淀给出答案:三菱软件智创未来畅享高效智能工业新体验,正在重塑工业生产全流程。
1. 编程效率拖后腿?软件工具链实现十倍速开发
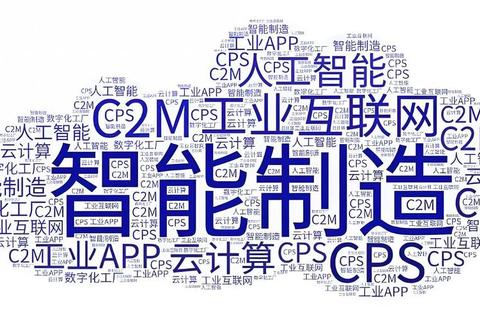
传统PLC编程需要工程师逐行编写梯形图,调试周期长达数周。三菱GX Works3通过三大创新彻底改变游戏规则:模块化编程将设备控制逻辑封装为可复用组件,上海三菱电梯利用该功能将电梯门机控制程序开发周期从45天缩短至7天;AI辅助纠错功能实时监测代码冲突,某锂电池厂商借此将调试错误率降低82%;3D虚拟调试技术让设备未出厂即可验证程序,广州某注塑机制造商因此减少80%现场调试时间。这套工具链使三菱软件智创未来畅享高效智能工业新体验真正落地,让工程师从代码劳工转型为系统架构师。
2. 设备孤岛难互联?智能中枢打通数据经脉
在苏州工业园,一条融合CC-Link IE TSN网络的智能产线正在颠覆传统。通过时间敏感网络技术,三菱将PLC、机器人、视觉系统的通信延迟控制在31微秒内,比传统总线快300倍。更关键的是其EdgeAccess2远程运维系统,当设备出现异常时,系统自动调取最近24小时运行数据,结合Maisart AI算法,佛山某陶瓷企业借此将故障诊断时间从平均4.5小时压缩至12分钟。这种软硬协同的解决方案,使三菱软件智创未来畅享高效智能工业新体验贯穿设备全生命周期。
3. 绿色转型成本高?能碳管家重塑生产逻辑
重庆某汽车零部件厂的能源管理革命颇具代表性。部署三菱E-JIT系统后,系统实时分析153个能耗节点的数据,通过动态调整空压机群组运行策略,单月节电达37万度。更值得关注的是其碳足迹追踪功能,从原材料采购到成品出库的全流程碳排数据可视化,助力企业获得国际碳关税优惠。这套系统已在全国23个工业园区复制,平均降低综合能耗19.8%,证明三菱软件智创未来畅享高效智能工业新体验的环保价值。
对于寻求转型的企业,建议分三步走:优先部署GX Works3提升底层控制效率,再引入CC-Link IE网络构建数据底座,最后加载能碳管理系统实现可持续发展。正如三菱自动化总裁张巍所言:"智能化不是推翻重来,而是让现有设备焕发新生"。当传统制造业插上智能软件的翅膀,降本增效与绿色转型将不再是非此即彼的选择题。