一、智能生产范式的系统性重构
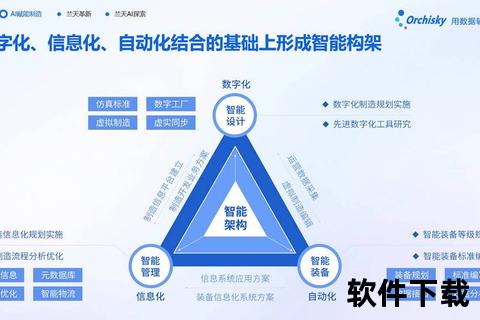
全维度AI软件通过整合机器学习、物联网与数字孪生技术,正在颠覆传统工业制造的底层逻辑。以全球灯塔工厂为例,其数据基础设施的早期投资已释放出显著价值:AI驱动的预测性维护系统将设备停机时间降低20%以上,智能排产算法使资源利用率提升30%。这种变革不仅体现在效率层面,更重塑了生产流程的决策机制——从经验驱动转向数据驱动,例如三菱电机的智能制造系统通过实时分析设备状态,自主优化维护周期,使设备寿命延长15%。
更深层的重构在于生产系统自进化能力的形成。传统制造依赖人工参数调整,而全维度AI系统具备动态学习能力:如华为工业AI质检平台通过800余种图像处理算子,使缺陷识别准确率达99.5%,且模型每季度迭代升级一次。这种持续优化的特性,使制造业首次实现“生产即学习”的闭环,为质量标准与工艺规范的动态演进奠定基础。
二、数据要素的价值网络构建
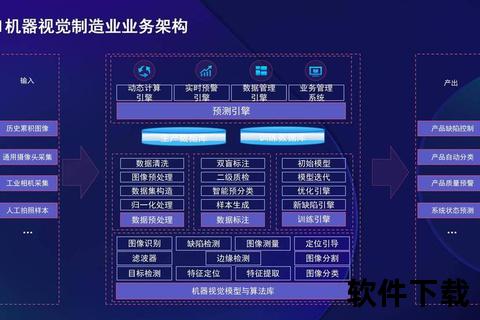
全维度AI软件的核心竞争力在于将工业数据转化为战略资产。卡奥斯工业大脑通过连接2000余家企业的设备数据,构建出覆盖研发、生产、物流的全域知识图谱,使新工厂AI模型部署周期从6个月缩短至3周。这种数据聚合效应打破传统工业的“信息孤岛”,形成跨工厂、跨产业链的协同网络。例如中国移动的“九天”平台,通过5G+AI实现设备数据毫秒级同步,使多工厂排产协调效率提升40%。
数据资产的深度挖掘更催生新型商业模式。思谋科技的工业互联网平台通过分析生产数据,为客户提供从设备健康管理到能耗优化的增值服务,其预测性维护系统使客户年度维护成本降低25%。这种从产品交付向服务赋能的转变,标志着制造业价值创造模式的历史性突破,数据要素成为比设备更核心的竞争力来源。
三、柔性制造体系的革命性突破
在个性化需求倒逼下,全维度AI软件重新定义制造柔性边界。Machina Labs的机器人工匠平台通过7轴机器人+AI流程模型,实现24小时内完成传统需3个月的产品迭代周期,其软件定义工厂模式使产线切换成本降低90%。这种敏捷性不仅体现在硬件层面,更在于智能决策系统的突破:山东大学团队开发的云边协同架构,使焊接工艺参数实时调整响应时间缩短至1秒,缺陷处理效率提升82%。
柔性制造的终极形态正在向自主演化方向发展。格创东智的设备健康管理系统,通过联邦学习技术实现跨工厂知识迁移,新产线调试周期从45天压缩至7天。这种能力使企业能够快速响应区域市场需求变化,例如某服装企业应用AI驱动的柔性供应链后,区域定制化订单交付速度提升3倍,库存周转率改善35%。
四、质量标准体系的智能化跃迁
传统质量控制在AI介入下发生质变。伟创力的智能焊接系统通过强化学习算法,使焊接参数自适应材料特性波动,产品不良率从0.8%降至0.05%。更革命性的是质量标准的动态生成机制:海尔卡奥斯平台通过分析10万+质检数据,自动优化检测标准阈值,使质量规范更新频率从年度级提升至实时级。
质量管控范畴也在AI驱动下扩展至全生命周期。美云智数的工艺仿真系统,通过数字孪生技术预测产品使用损耗,提前优化设计参数,使某家电产品返修率降低60%。这种预防性质量工程理念,将质量控制从制造环节延伸至研发端,形成覆盖产品全生命周期的质量保障网络。
五、产业生态协同的指数级进化
全维度AI软件正在重构制造业生态关系。研华科技的边缘AI解决方案通过开放API接口,使上下游企业数据共享效率提升5倍,产业链协同创新周期缩短50%。这种生态化反效应在汽车行业尤为显著:某整车厂通过AI协同平台整合200余家供应商数据,使新车研发周期从36个月压缩至22个月。
更深层的变革在于价值分配机制的重塑。洛克希德·马丁投资的Machina Labs采用DEV SUITE模式,允许客户按需调用AI制造能力,使中小企业创新门槛降低70%。这种“制造即服务”模式打破规模经济壁垒,使产业生态从链式结构向网状协同进化,为制造业创新注入全新活力。
当工业文明迈入智能纪元,全维度AI软件不仅重新定义了制造标准,更在深层次重构产业价值网络。从数据资产的觉醒到生态协同的裂变,这场变革正在突破物理工厂的边界,催生“软件定义制造”的新范式。未来,随着量子计算与神经拟态芯片的融合,工业智能系统或将具备自主进化能力,届时制造标准的动态迭代将真正实现“实时响应需求,瞬时优化系统”的终极目标。企业唯有构建开放、敏捷的AI赋能体系,才能在智能制造的新赛道上赢得先机。