一、传统工业转型:效率瓶颈如何突破?
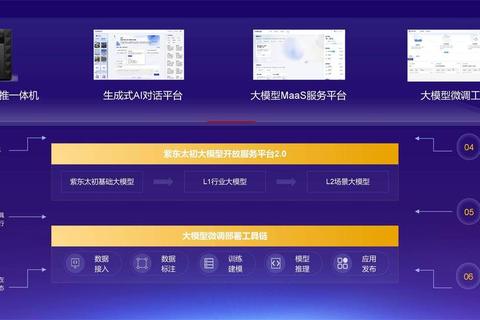
全球制造业正面临智能化升级的迫切需求,但许多企业在转型中陷入困境:高昂的硬件投入、复杂的编程逻辑、低效的系统协同,导致自动化改造进展缓慢。据国际机器人联合会统计,2024年全球仍有43%的制造企业因技术门槛放弃智能化升级。在此背景下,欧姆龙通过创新融合其编程软件,以「结构化编程+模块化设计」为核心,高效赋能智能自动化转型新浪潮。
二、突破开发效率:编程软件如何简化复杂流程?
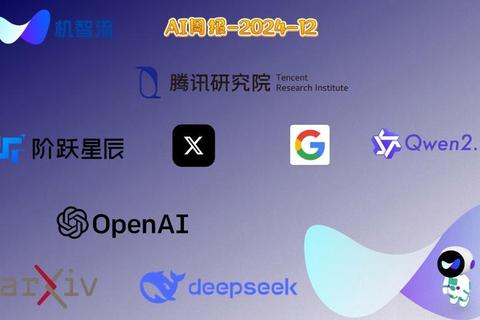
在汽车总装产线的自动化改造中,某企业曾面临编程耗时长的难题:传统梯形图编程需手动调试2000个逻辑节点,平均耗时480小时。而采用欧姆龙CX-Programmer软件的ST语言功能后,工程师通过结构化文本编程,将重复代码封装为函数块,开发周期缩短至120小时,效率提升300%。
典型案例:某新能源汽车电池生产线引入欧姆龙NJ系列PLC,利用Sysmac Studio平台的多语言混合编程功能(梯形图+ST语言+功能块),仅用3周完成原需2个月的视觉检测系统开发。数据显示,其代码复用率从15%跃升至65%,调试时间减少40%。
三、赋能智能优化:数据驱动如何提升系统性能?
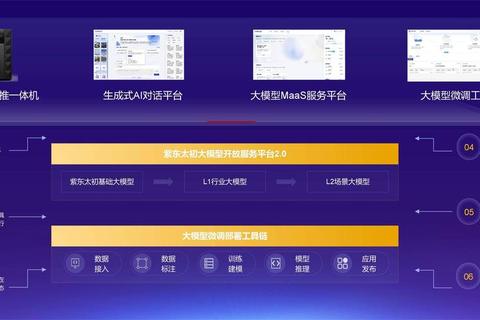
欧姆龙编程软件的「数据感知-分析-决策」闭环能力,成为智能工厂的核心引擎。以西班牙HIPRA疫苗工厂为例,其部署的LD-90移动机器人通过欧姆龙PLC与Sysmac平台深度集成,实时采集设备运行数据,结合AI算法预测物流路径冲突,使物料运输效率提升25%,故障响应时间缩短至10秒内。
技术亮点:
动态参数调整:通过PLC内置的PID控制器与实时数据库联动,实现生产线温控精度±0.5℃(传统系统为±2℃)
预测性维护:利用FINS协议采集设备振动数据,提前14天预警电机故障,维护成本降低30%
四、构建生态协同:跨平台集成如何打破信息孤岛?
在某半导体巨头的智能工厂项目中,欧姆龙通过「PLC+MES+ERP」三级架构实现全链路协同:
1. PLC层:CP1H系列控制器采集2000+传感器数据,处理速度达0.1ms/指令
2. 中间层:CX-Integrator工具将生产数据同步至SAP MES系统,延迟低于50ms
3. 决策层:与ERP系统联动生成动态排产方案,库存周转率提升18%
行业验证:该方案使设备综合效率(OEE)从76%提升至89%,能源消耗降低22%,被国际自动化协会评为「2024年度最佳工业4.0实践案例」。
五、转型路径建议:企业如何把握升级机遇?
对于不同规模企业,可参考以下实施路径:
1. 中小型企业:优先采用欧姆龙CP系列PLC+CX-One基础套件,通过预置的50种工艺模板快速部署(成本可控制在20万元内)
2. 大型集团:部署NJ系列控制器+Sysmac AI模块,结合数字孪生技术实现全厂级仿真优化
3. 人才培养:参加欧姆龙认证工程师计划(全球已培养12万名技术专家),掌握ST语言编程与数据分析技能
创新融合欧姆龙编程软件高效赋能智能自动化转型新浪潮的实践表明,技术突破必须与业务场景深度融合。正如某汽车零部件企业CTO所言:「不是选择最先进的技术,而是选择最适合的解决方案。」在智能化浪潮中,企业需以数据为纽带,以软件为桥梁,方能实现从「制造」到「智造」的跨越式发展。